We all know that reducing oxidative loss on the external surface of graphite electrodes is an effective approach to decrease electrode consumption.
Presently, both domestic and international factories have adopted an anti-oxidation coating process to mitigate the consumption of graphite electrodes. This method involves applying a layer of aluminum and refractory material on the electrode surface through a technique known as alternating spray smelting. The key steps of this process entail initially creating shallow grooves on the exterior surface of the graphite electrode. Subsequently, the electrode is heated to approximately 250°C within a heating furnace. A thin layer of aluminum is sprayed onto the electrode’s surface using a metallic spray gun, followed by applying a refractory slurry onto the outer side of the aluminum layer. Ultimately, the high temperature generated by the electric arc fuses the aluminum and refractory slurry together, forming a conductive and high-temperature oxidation-resistant metal-ceramic layer.
The performance requirements of this anti-oxidation coating are as follows:
- Electrical resistivity between 0.07-0.1 Ωm;
- Gas impermeability duration exceeding 50 hours at 900°C;
- Coating decomposition temperature above 1850°C.
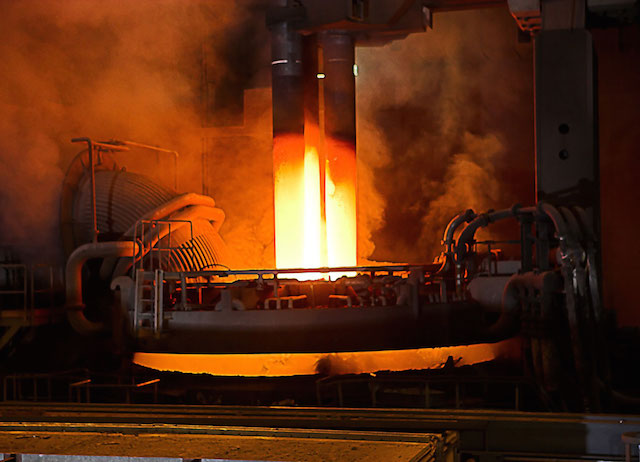
Through testing, it has been established that compared to graphite electrodes of the same quality but lacking anti-oxidation coatings, coated electrodes can reduce net electrode consumption per ton of electric furnace steel by 20% to 30%, and power consumption per ton of steel by approximately 5%. When employing anti-oxidation coated graphite electrodes in electric arc furnace steel plants, modifications to the electrode holder are necessary. The inner diameter of the holder should be suitably enlarged, and a few arc-shaped graphite pads should be embedded to facilitate current conduction through the graphite electrode via the pads. Direct contact between the anti-oxidation coating and the graphite electrode holder can lead to electric sparks on uneven contact surfaces, potentially damaging the holder.