Impregnation is a process of reducing the pores of graphite electrodes, increasing the density, increasing the compressive strength, reducing the resistivity of the finished product, and changing the physical and chemical properties of the product.
Maintaining a good rheological state of the impregnating asphalt during the impregnation process is the key to improving the impregnation effect, and the reduction of the viscosity of the impregnating asphalt is achieved by increasing the impregnating temperature. The main purpose of controlling the impregnating temperature is to reduce the viscosity of the impregnating asphalt , increase the impregnation amount of asphalt and improve the impregnation effect. In the current industrial production, the temperature when the viscosity of the impregnating agent asphalt is 100mPa·s is generally taken as the impregnating temperature. The impregnating temperature can be determined according to the viscosity-temperature curve of the impregnating agent asphalt.
Appropriately increasing the heating temperature can reduce the viscosity of the impregnating agent asphalt and improve the fluidity of the asphalt. Generally, it is more appropriate to maintain the impregnating temperature at 180~200°C. If the impregnating temperature is too high, it will not only decompose the impregnating asphalt, resulting in a decrease in the negative pressure in the matrix, but also reduce the effective pressure applied to the impregnating asphalt.
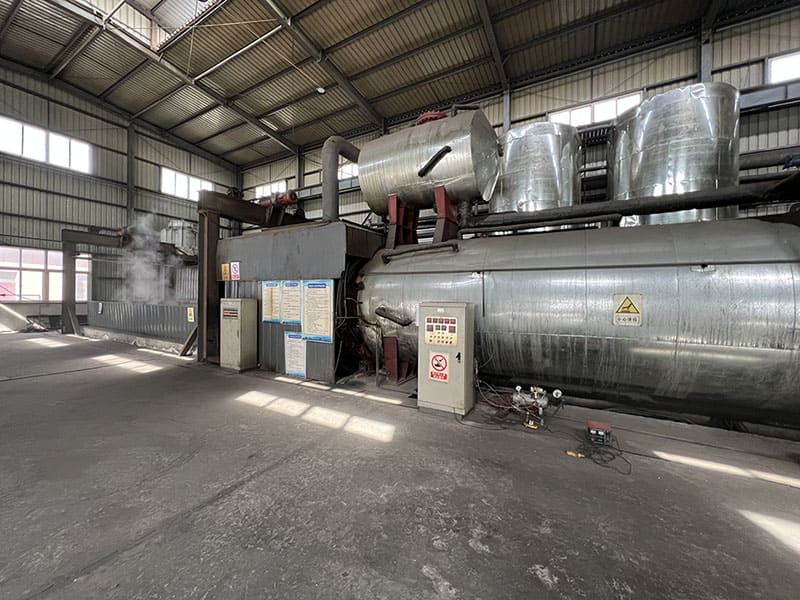
Appropriately increasing the heating temperature can reduce the viscosity of the impregnating agent asphalt and improve the fluidity of the asphalt. Generally, it is more appropriate to maintain the impregnating temperature at 180~200°C. If the impregnating temperature is too high, it will not only decompose the impregnating asphalt, resulting in a decrease in the negative pressure in the matrix, but also reduce the effective pressure applied to the impregnating asphalt.
Impregnation should be carried out at the temperature with the lowest viscosity of the asphalt. Therefore, the melting temperature of the impregnating asphalt should be 160~200°C, so as to ensure that the fluidity of the impregnating asphalt is in a good state, the viscosity is relatively low, and it is easy to penetrate into the pores of the carbon billet middle. However, if the temperature of the impregnating agent asphalt is too high, it will also decompose a large amount of asphalt and emit volatile matter during the impregnation process, making the impregnation effect worse.

How to determine the preheating temperature of the impregnation tank?
In order to ensure that the impregnating asphalt maintains good rheological properties during impregnation, the impregnation tank should also be preheated to 150~180°C before loading the impregnated carbon billet. If the temperature of the impregnating tank is low, the viscosity of the impregnating agent asphalt will be reduced during impregnation, thus making the impregnation effect worse.
How to determine the impregnation pressure and pressurization time?
The impregnation is realized by pressurizing the liquid pitch, and the impregnation operation of the carbon material is carried out under a certain pressure. Since bituminous liquids have incompressible parts, changes in pressure undoubtedly have a significant effect on the penetration capacity of molten bitumen.
The impregnation pressure for small and medium-sized carbon billets with low density can be maintained at about 0.8Mpa; , the pressing pressure must be increased to 1.0~1.5MPa; for fine-grained carbon billets with high density, the impregnation pressure should be increased to 2.0~4.0MPa and the pressing time is generally 2~4h. The time is about 2 to 4 hours; and for large-scale carbon billets, the pressurization time should be more than 3 hours.
In conclusion, the precise determination of the optimal temperature and melting point of pitch is crucial for achieving high-quality graphite electrodes during the impregnation process. By carefully controlling these parameters, manufacturers can enhance the electrodes’ mechanical strength, electrical conductivity, and overall performance. Consistency in temperature and melting point leads to efficient impregnation and minimized defects. By applying the knowledge gained from this article, manufacturer can optimize their impregnation process and produce superior graphite electrodes that meet the stringent requirements of various industries.